Major polluting industries, such as thermal power plants, iron and steel factories, and cement production facilities, stand as formidable contributors to environmental degradation on a global scale. These industrial sectors, vital for economic development and infrastructure growth, are often characterized by the release of significant quantities of pollutants into the air, water, and soil, posing grave threats to human health and ecosystems. The combustion of fossil fuels in thermal power plants emits greenhouse gases and particulate matter, exacerbating climate change and air quality issues. Similarly, iron and steel manufacturing processes release harmful gases and heavy metals, while cement production contributes to air pollution through the emission of carbon dioxide and other pollutants. Understanding the environmental impacts of these industries is imperative for implementing effective mitigation strategies and transitioning towards more sustainable practices to safeguard the planet for future generations.
Contents
- 1 THERMAL POWER PLANTS
- 2 IRON AND STEEL INDUSTRY
- 3 CEMENT INDUSTRIES
- 4 TEXTILES INDUSTRIES
- 5 PETROCHEMICAL INDUSTRIES
- 6 PETROLEUM REFINING
- 7 FAQs: Thermal Power Plants
- 7.1 1. What is the significance of thermal power plants in India’s electricity generation?
- 7.2 2. How do thermal power plants generate electricity?
- 7.3 3. What are the different categories of thermal power plants based on heat sources?
- 7.4 4. What are the primary types of thermal power plants in India, and what is their installed capacity?
- 7.5 5. What factors have contributed to the growth of the Indian steel sector?
- 7.6 6. What is the current and projected crude steel production in India?
- 7.7 7. How is the capacity distributed between the private and public sectors in the cement industry?
- 7.8 8. How has cement production in India evolved over the years?
- 8 In case you still have your doubts, contact us on 9811333901.
THERMAL POWER PLANTS
- Thermal power plants play a pivotal role in contributing the largest share of electricity to India’s national power grid.
- Operating on the principle of harnessing heat from various fuel sources, these plants generate electricity through a process that typically involves creating steam in a boiler, driving a steam turbine, and ultimately powering a generator.
- Thermal power plants are categorized based on their heat sources, encompassing coal-fired, gas, diesel or liquid fuel, geothermal, biomass, and waste material.
- In India, the primary reliance is on three types of thermal power plants, each with its installed capacity as of January 2021:
- Coal: 206,404.50 MW
- Gas: 24,956.51 MW
- Liquid Fuel (Diesel): 509.71 MW
- The cumulative capacity of thermal power plants across India, as of January 31, 2021, stands at 231,870.72 MW. Notably, these thermal power plants collectively contribute 71% of the total power generation in the country.
IRON AND STEEL INDUSTRY
- India ranked as the world’s second-largest steel producer in 2018, following China.
- The growth of the Indian steel sector has been fueled by the abundant domestic availability of raw materials, particularly iron ore, and a cost-effective labor force.
- This has positioned the steel industry as a significant contributor to India’s overall manufacturing output.
- In 2018, India’s crude steel production reached 106.5 million tonnes (MT), reflecting a 4.9 percent increase from the previous year’s production of 101.5 MT.
- The Indian steel industry is categorized into major producers, main producers, and secondary producers.
- Projections indicate that India is on track to surpass the USA and become the world’s second-largest steel consumer in 2019. According to the Indian Steel Association (ISA), steel demand in India is expected to grow by over 7 percent in both the fiscal years 2019-20 and 2020-21.
- In the fiscal year 2018-19, India achieved a production of 131.57 million tonnes (MT) of gross finished steel and 106.56 MT of crude steel.
- Export and import figures for finished steel stood at 2.45 MT and 3.35 MT, respectively, in the fiscal year 2019-20 up to August.
- The National Steel Policy 2017, launched by the government, aims to boost per capita steel consumption to 160 kgs by the year 2030-31.
- Additionally, the National Mineral Development Corporation plans to invest US$ 1 billion in infrastructure over the next three years to enhance iron production.
- According to the Economic Survey 2018-19, steel production is anticipated to reach 128.6 million tonnes by the year 2021.
CEMENT INDUSTRIES
- India holds the position of being the world’s second-largest cement producer.
- By July 2019, the country had produced 28.08 million tonnes of cement, with expectations that the production capacity would reach 550 million tonnes by 2020.
- The private sector accounts for a substantial 98 percent of this total capacity, leaving the remaining 2 percent in the hands of the public sector.
- Among the 210 large cement plants across India, 77 are strategically located in states such as Andhra Pradesh, Rajasthan, and Tamil Nadu.
- Over the years, India has witnessed significant growth in cement production, escalating from 230.49 million tonnes in the fiscal year 2011-12 to a notable 297.56 million tonnes by the fiscal year 2017-18.
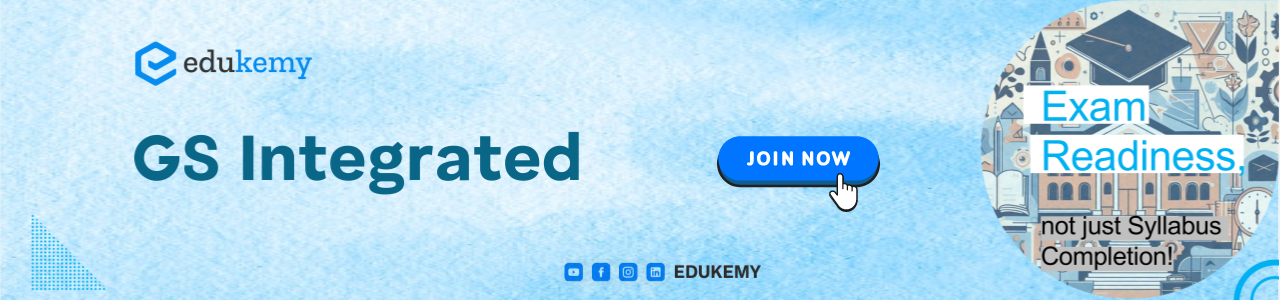
TEXTILES INDUSTRIES
- India’s textiles sector holds a historic significance, being one of the oldest industries in the country with roots dating back several centuries.
- During the fiscal year 2017-18, India’s textile exports reached US$ 39.2 billion. This figure is anticipated to witness substantial growth, reaching US$ 82.00 billion by 2021, compared to US$ 31.65 billion in FY19.
- Currently valued at approximately US$ 150 billion, the Indian textiles industry is projected to reach US$ 250 billion by 2019.
- In terms of industry output (value), it contributed seven percent to India’s overall industrial production in 2017-18. Additionally, the sector contributed two percent to the country’s Gross Domestic Product (GDP) and provided employment to over 45 million people during the same fiscal year.
- In the export arena, the textiles industry made a substantial contribution, accounting for 15 percent of India’s total export earnings in 2017-18.
- As part of supporting this crucial sector, the Indian government has introduced various export promotion policies.
- Notably, it has permitted 100 percent Foreign Direct Investment (FDI) in the Indian textiles sector through the automatic route.
- India proudly stands as the world’s second-largest exporter of textiles and clothing, showcasing the global significance and competitiveness of its textile industry.
PETROCHEMICAL INDUSTRIES
- Various products are derived from crude petroleum, serving as raw materials for a multitude of new industries. These collectively fall under the umbrella term “petrochemical industries.”
- Petrochemical industries are broadly classified into polymers, synthetic fibers, elastomers, and surfactant intermediate industries. Among the prominent locations for these industries, Mumbai stands out as a central hub.
- In the petrochemical sector, three organizations operate under the administrative control of the Department of Chemicals and Petrochemicals:
- The Indian Petrochemical Corporation Limited (IPCL)
- The Petrofils Cooperative Limited (PCL)
- The Central Institute of Plastic Engineering and Technology (CIPET)
- Additionally, the National Organic Chemicals Industries Limited (NOCIL) holds a significant position in the petrochemical landscape, established as a private sector entity in 1961.
PETROLEUM REFINING
- Petroleum refineries are expansive industrial complexes with numerous processing units and auxiliary installations, including utility units and storage tanks.
- The configuration and combination of processes within each refinery are unique, influenced by factors such as the refinery’s location, target products, and economic considerations.
- An oil refinery, or petroleum refining facility, is where crude oil undergoes extraction and transformation into valuable products such as petroleum naphtha, gasoline, jet fuel, asphalt foundation, heating oil, petroleum kerosene, and liquefied gas. These refineries are typically vast industrial facilities featuring extensive pipelines that facilitate the transportation of fluid streams between different units.
- Petroleum is a complex mixture containing various substances like gas, petrol, diesel, kerosene, lubricating oil, and paraffin wax. Given the diverse purposes these constituents serve, it becomes essential to separate or refine crude oil.
- This process of separation is known as petroleum refining, and it involves a three-step process.
- The first step is separation, where crude oil is subjected to distillation, causing it to separate into different components.
- Heavier constituents settle at the bottom, while lighter ones rise as vapor or remain in liquid form.
- The next step is conversion, where the heavier constituents are transformed into gas, gasoline, and diesel.
- However, these products may still contain impurities.
- Hence, the final step involves treating them to eliminate impurities and obtain pure forms of the various refined products.
- In summary, petroleum refining is a multi-step process involving separation, conversion, and treatment to produce a range of valuable petroleum products.
FAQs: Thermal Power Plants
1. What is the significance of thermal power plants in India’s electricity generation?
A: Thermal power plants play a crucial role in contributing the largest share of electricity to India’s national power grid, supplying energy to meet the nation’s power demands.
2. How do thermal power plants generate electricity?
A: Thermal power plants generate electricity by harnessing heat from various fuel sources, typically involving the creation of steam in a boiler, driving a steam turbine, and powering a generator.
3. What are the different categories of thermal power plants based on heat sources?
A: Thermal power plants are categorized into coal-fired, gas, diesel or liquid fuel, geothermal, biomass, and waste material plants, depending on the heat source they utilize.
4. What are the primary types of thermal power plants in India, and what is their installed capacity?
A: India mainly relies on three types of thermal power plants:
- Coal: 206,404.50 MW
- Gas: 24,956.51 MW
- Liquid Fuel (Diesel): 509.71 MW
- The total installed capacity of thermal power plants in India, as of January 31, 2021, is 231,870.72 MW.
5. What factors have contributed to the growth of the Indian steel sector?
A: The growth of the Indian steel sector is attributed to abundant domestic availability of raw materials, particularly iron ore, and a cost-effective labor force.
6. What is the current and projected crude steel production in India?
A: In 2018, India’s crude steel production was 106.5 million tonnes (MT), and projections indicate a production of 128.6 million tonnes by 2021.
7. How is the capacity distributed between the private and public sectors in the cement industry?
A: The private sector holds 98% of the total cement production capacity, while the public sector accounts for the remaining 2%.
8. How has cement production in India evolved over the years?
A: Cement production in India has grown significantly, escalating from 230.49 million tonnes in the fiscal year 2011-12 to 297.56 million tonnes by the fiscal year 2017-18.
In case you still have your doubts, contact us on 9811333901.
For UPSC Prelims Resources, Click here
For Daily Updates and Study Material:
Join our Telegram Channel – Edukemy for IAS
- 1. Learn through Videos – here
- 2. Be Exam Ready by Practicing Daily MCQs – here
- 3. Daily Newsletter – Get all your Current Affairs Covered – here
- 4. Mains Answer Writing Practice – here