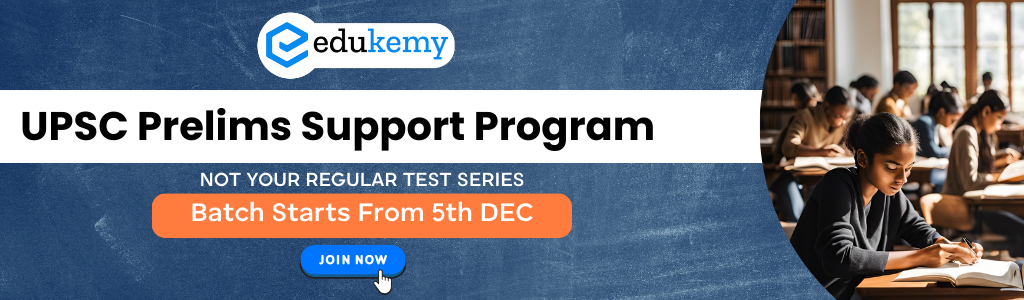
Contents
- 1 Q1. Identify the important periods of industrialisation in India and analyse the character of its two most developed industrial regions. (1993)
- 2 Q2. Trace the evolution of industries in India and evaluate the role of multinational and liberalisation policies in this context. (2006)
- 3 Q3. Analyse the role of policy of liberalisation on industrial landscape of India. (2002)
- 4 Q4. Describe the growth, characteristics and distribution patterns of India’s industrial regions. (2001)
- 5 Q5. Discuss the growth location and distribution of iron and steel Industry in India. (2000)
- 6 Q6. Discuss the factors for the localisation of either the Cement or the Cotton textile industry in India and analyse the pattern of its distribution. (1999)
- 7 Q7. Examine the importance of industrial estates in India. (1998)
- 8 Q8. Bring out the trends in the development of fertilizer industry in India. (1998)
- 9 Q9. Growth of agro-based industries in Uttar Pradesh and Bihar. (1998)
- 10 Q10. Critically examine the locational pattern and trend of production of forest-based industries in India. (1997)
- 11 Q11. Analyse the factors for the localization of either the cotton textile or the sugar industry in India and note the recent trends in the industry. (1997)
- 12 Q12. Recent changes in India’s basic industrial policy. (1995)
- 13 In case you still have your doubts, contact us on 9811333901.
Q1. Identify the important periods of industrialisation in India and analyse the character of its two most developed industrial regions. (1993)
Answer :
India was an industrially developed country before the advent of industrial revolution in Europe. But after the industrial revolution, Indian handicrafts and products of village industries could not compete with the factory products of Britain. And thus the household industries of the country gradually declined.
The important periods of industrialisation in India can be identified under the following headings:
Pre-Independence Industrial Development: The history of modern industrialisation in India started with the establishment of cotton textile mill in Mumbai in 1854. First jute mill was started at Rejra near Kolkata in 1855. Coal mining, paper mill and chemical industries were also started. With the establishment of TISCO at Jamshedpur in 1907, a new chapter in the industrial history of India was opened.
The growth of industry before the First World War was slow and holding. Both the world wars gave impetus to industrial development as India became the source of supply for allied operations east of suez. The post-war decreased demand, inflation and the partition of the country in 1947 adversely affected industries, especially jute and cotton textile.
Post-Independence Industrial Development: On the eve of independence, the industrial development in India was confined largely to consumer goods; important industries being cotton textile, sugar, soap, leather goods and paper. The growth of manufacturing and capital goods industry was slow and lagging. The 1948 Industrial Policy Resolution defined the broad contours of the industrial policy and delineated the role of the state in industrial development both as an entrepreneur and as an authority. The concept of mixed economy was introduced by this policy. Later on, the Industrial Policy Resolution of 1956 gave the public sector a strategic role in the economy with the aim of speeding up industrialisation, developing heavy industries and preventing monopoly.
The industrial growth has not been uniform since 1951. After a stready growth of about 8% during the initial period of 14 years (1951-65). There was fluctuating trend since then. In the sixties the average growth rate of industrial output was put at 5.5% and in the seventies the average growth rate has been about 4%/year. The growth rate was again 5.5% during 1980-85. It picked up to 8.48% between 1985-90 but slowed down to 5.3% between 1990-95. As a result of economic crisis of 1990-91, wide ranging reform measures leading to liberalisation, privatisation and globalisation were taken which gave boost to the industrial production. The government is taking a number of measures to accelerate the rate of industrial growth.
Character of the two most developed industrial regions has been analaysed below:
1.Mumbai-Pune Industrial Region: It extends from Thane to Pune and in adjoining districts of Nashik and Sholapur. Besides, industrial development has been rapid in Kolaba, Ahmednagar, Satara, Sangli and Jalgaon districts. Development of this region started with the location of cotton textile industry in Mumbai. Mumbai had favourable locational advantages for the cotton textile industry. Opening of the Suez canal in 1869 provided impetus to the growth of Mumbai port. Machinery were imported through this port. Hydroelectricity was developed in the western ghat region to meet the requirements of this industry.
With the development of cotton textile industry, chemical industry also developed. Opening of the Mumbai High Petroleum field and erection of nuclear energy plants added additional magnetic force to this region.
Besides, engineering goods, petroleum refining, petrochemicals, leather, synthetic and plastic goods, drugs, fertilisers, electrical, electronics, shipbuilding, software, transport equipments and food industries also developed. Important industrial centres are Mumbai, Kolaba, Kalyan, Thane, Trombay, Pune, Pimpri, Nashik, Manmad, Solapur, Ahmednagar, Satara and Sangli.
2.Gujarat Industrial Region: The nucleus of this region lies between Ahmedabad and Vadodara. Development of this region is also associated with the location of the cotton textile industry since 1860s. This region became an important textile region with the decline of the cotton textile industry in Mumbai. Located in cotton growing area, this region has double advantage of the proximity of raw materials as well as of market of the densely populated Ganga plain. The discovery of the oil fields led to the development of a variety of petrochemical industries around Ankleshwar, Vadodara and Jamnagar. The port of Kandla helped in the rapid growth of this region. The industrial structure is now diversified. Besides textiles and petrochemical industries, other industries are heavy and basic chemicals, motor, tractor, textile machinery, engineering, pharmaceuticals, sugar, dairy products and food processing. Recently largest refinery has been set up at Jamnagar. Important industrial centres of this region are Ahmedabad, Vadodara, Bharuch, Koyali, Anand, Khera, Rajkot, Surat, Valsad and Jamnagar.
Q2. Trace the evolution of industries in India and evaluate the role of multinational and liberalisation policies in this context. (2006)
Answer :
All the developed countries of the world have highly developed and diversified industrial sectors. India was an industrially developed country before the advent of industrial revolution in Europe. Indian Industry was integrated with its agriculture and house-hold industries were an integral part of the national economy.
Pre-Independence Industrial Development: The history of industrialisation in India started with the establishment of cotton textile mill in Mumbai in 1854. First jute mill was started at Risra. Coal mining in the Chhotanagpur region also began about the same time, subsequently, paper mill and chemical industries were set up. The big Iron industry was started at Kulti in 1875. With the Tata Iron and Steel Company at Jamshedpur in 1907,a new chapter in the industrial history of India opened up. Numerous industries came up such as steel, sugar, cement, glass; these industries expanded during this period.
Post-Independence Industrial Development: On the eve of Independence, the industrial development in India was confined largely to consumer goods, important industries being cotton textile, sugar, salt, soap, leather goods and paper. The 1948 Industrial Policy Resolution defined the broad contours of the industrial policy.
The process of industrialisation started withthe launching of the First Five year Plan (1951-56). The main emphasis was on fuller utilisation of existing capacity. A number of industries were set up. Newsprint, calcium carbide, penicillin, motor and transformer of higher rating were manufactured for the first time in the country during the first plan.
The Industrial Policy Resolution of 1956 gave the public sector a strategic role in the economy and the main emphasis was laid on the expansion of capital and producer goods industries. Three new steel plants were established.
Foundations were laid for heavy electrical and heavy machine tools industries and many other branches of heavy engineering industries. During the Fourth Plan efforts were made to remove imbalances in industrial development and to increase production of goods for exports and for further industrialisation. During the Fifth Plan the rise in petroleum prices created economic crises.
During Sixth Plan (1980-85) industrial policy was liberalised, production started picking up and electronic industry witnessed phenomenal growth. The Seventh Five Year Plan (1985-90) evolved an Integrated Industrial Policy to concentrate on development of industries with large domestic market and export potential. New Industrial Plan of 1991 announced several liberalisation measures and the subsequent Eighth Five Year Plan (1992-97) emphasised privatisation and liberalisation for industrial growth.
Type of Industries:
Industries are classified in a number of ways. On the basis of size, capital investment and labour force employed, industries are classified into large scale, medium scale and small scale. Industries are also classified on the basis of the use of their products such as (1) basic goods industries, (2) capital goods industries, (3) intermediate goods industries and (4) consumer goods industries.
Industries are classified also on the basis of raw materials: (1) agriculture based industries, (2) forest based industries, (3) mineral based industries and (4) processed raw material based industries.
Another common classification of industries is based on the nature of manufactured products. Eight classes of industries are: (1) Metallurgical industries, (2) Mechnical engineering, (3) Electrical engineering, (4) Chemical and Allied Industries, (5) Textile Industries, (6) Food Industries, (7) Electricity Generation, (8) Electronics and Communication Industries.
Location of an industry is influenced by several factors. Among them, access to raw materials, power, market, capital, transport and labour are important. A new Industrial Policy was announced in 1991. This policy deregulated the industrial economy in a substantial manner. Major objectives of the new policy were to build on the gains already achived and maintain a sustained growth in productivity and gainful employment along with attaining international competitiveness. The policy has three main dimensions – liberalisation, privatisation and globalisation.
Role of Multinationals: Globalisation means interacting the economy of the country with the world economy. The process of globalisation has been to increase the domestic and external competition through extensive application of market mechanism and facilitating forging investors and supplies of technology.
The process of globalisation started in eighties itself when many concessions were granted to foreign investors. Multinationals were allowed to enter in sectors including defence to which their entry was previously restricted. The system of licensing has been made very liberal. In the Indian context, this implies:
- opening far the foreign companies to invest in different fields of economic activity.
- The entry of multinational companies in India.
- Allowed Indian companies to enter into foreign collaboration in India and also encouraging them to set up joint ventures abroad.
- Set of export incentives like exchange rate adjustments for promoting export.
The new economic policy was introduced by Government of India in July 1991. Certain steps have been taken towards globalisation. Indian rupee has been made fully convertible on current account.
Indian import policy allows the free import of all items including capital goods except a negative list.
Various incentives and facilities have been offered to the foreign investors and non-resident Indians for direct foreign investment.
Liberalisation: Major liberalisation measures announced are: (1) abolition of industrial licensing, (2) Free entry to foreign technology, (3) foreign direct investment policy,(4) access to capital market, (5) open trade, (6) abolition of phased manufacturing programme, (7) liberalised industrial location programme and (8) Indian rupee has been made fully convertible on current account.
The Industrial licensing system has been abolished for all items except three industries related to security,strategic or environmental concerns. Number of industries reserved for the public sector since 1956 has been reduced from 17 to only 4.
Government has also decided to offer a part of government shareholdingin the public sector enterprises to financial institution, general public and workers.
As in the case of domestic investment, foreign investment has also been traditionally regulated in India. Foreign Direct Investment is seen as a means to support the domenstic investment for achieving a higher level of economic development.
Foreign Direct Investment: Automatic approval route in most of the sectors has been introduced.
Govt. has also announced changes in existing industrial location policy. Industrial location is discouraged only in large cities because of environment reasons. under the new industrial policy, an industrial licence is required when the project involves manufacture of an item which is on the list. Industrial policy has been liberalised to attract private investorsboth domestic and multinational corporation. New sectors like mining, banking , telecommunication, highway construction and management have been thrown open to private companies.
However, with increasing foreign investment a number of undesirable features of multinational corporations are notable. Joint venture of Indian companies with foreign firms have not always been advantageous.
Demerits of MNC:
- The impact of MNCs on the development of a country is highly uneven in many situations. These enterprises widen the already high income gap between the rich and the poor.
- They tend to promote the interest of small number of well-paid modern sector workers, and this leads to the widening of wages differentials in the country.
- MNCs are located mostly in urban areas.
- MNCs improve the foreign exchange position of a country. However, their long-term impact may reduce foreign exchange earning of both current and capital accounts. Finally on the basis of empirical research of the part performance of multinational companies in India, it has been suggested that their net contribution to the Indian economy has often been negative.
- Most of these MNCs have emerged in specific sectors like IT-industry only at the cost of neglect of other secondary and tertiary sectors.
Q3. Analyse the role of policy of liberalisation on industrial landscape of India. (2002)
Answer :
Liberalisation policy was adopted to bring about rapid and substantial improvement in the quality of life of the people of India, rapid growth in income levels, for full utilization of our material and human resources, making Indian industries globally competitive and effecient, coming of foreign technology and skill into Indian industries.
Most of the big industries in India before 1991 were public sector undertakings which were either raw material oriented or for backward area development. For example, most of the iron and steel industries like Jamshedpur, Bokaro, Raniganj, Bhadravati, etc. were based on availability of raw material source, while Bhilai was installed for backward area development. The oil refinery of Barauni in Bihar was installed for the same purpose. Thus, the industrial landscape looked raw material oriented or market oriented, as was the case in the industrial regions of Mumbai and Kolkata. Also productwise, industries were mostly indulged in producing specific goods, demanded in the Indian market.
Now, the industrial landscape is witnessing a locational shift. From raw material oriented, it is now becoming more of export oriented and mostly market oriented. Those regions with better infrastructure are attracting industries as the private sectors have nothing to do with public service. The Mumbai, Delhi, Gujarat plain regions are flourishing new ports like Paradweep, Ennure, Nahvasheva are coming up for export purposes. With the approval of SEZs (Special Economic Zones) and AEZ (Agriculture Export Zone), the industrial landscape is changing.
Export oriented industrial centres like Paradweep, Vishakhapattanam, Gopalpur, etc. are coming up repidly. From raw material processing our industries are doing precission work also. Emergence of petrochemical complexes on the industrial map is also a significant change. The recent discovery of natural gas in the Krishna-Godavari delta by Reliance Company will add new dimension to the industrial landscape.
Q4. Describe the growth, characteristics and distribution patterns of India’s industrial regions. (2001)
Answer :
Industries are not distributed evenly in India, since the factors affecting the industrial location are not the same everywhere. Industries tend to concentrate in few pockets due to certain favourable factors. The pockets having high concentration of industries are known as Industrial Regions.
In India, the industrial development on modern scientific lines is of very recent origin. It is after independence through Five Years Plans that emphasis was placed on the development of heavy and basic industries and consumer industries. In reality, the country still lacks well marked industrial belt with heavy concentration of industries similar to Europe, U.S.A. or Japan. Only there are industrial clusters of different sizes mainly located around the premier part of cities which played pivotal role during the colonial period.
Several attempts have been made to delineate the industrial regions of India making use of different criteria. On the basis of size and industrial activity a distinction has been made between major and minor industrial regions. Following is the most widely accepted schemes of dividing India into major industrial regions:
(1) The Hugli Industrial Region: This is the most important industrial region in eastern India extending from Naihati to Budge along the left bank and from Tribeni to Nalpur along the right bank of the Hugli river. Kolkata is the main centre of the region.
This region had following advantages that have helped it to become a major industrial region:
- The early development of Calcutta as a trading centre and later as the seat of administration attracted large British investment.
- Calcutta being both riverine and sea port provided access to the raw materials found in the hinterland and made easy the export and import of finished goods and inputs.
- The rich fertile soil made the region agriculturally very rich and so agro-raw material like jute, cotton, silk, tea-indigo were abundantly available.
- The region was situated close to the mineral rich region of Chhotanagpur.
- Cheep labour could be found easily from the thickly populated states of Orissa, Bihar and U.P.
- Calcutta plus the extensive hinterland provided a large market.
- A good network of rail, road and water ways developed in this region which connected it to adjoining regions.
The discovery of coal and iron in Chhotanagpur plateau, tea plantations in Assam and northern west Bengal and the processing of deltaic Bengal’s jute led to the industrial development in Hugli region. A chain of jute mills and other factories could be established on either side of Hugli region was responsible for two-thirds of factory emplyment in India.
After the partition of India and Pakistan the region faced the problem of jute storage which was solved later on by gradually increasing home production. The construction of the Farakka barrage and flushing of the channel were the only possible answers to the problem of the silting of the Hugli river which was posing problem for the big ships to come in.The construction of Haldia port is another landmark in relieving the pressure on the Kolkata port. The reclamation of salt lake area for the city expansion, increasing the output of electricity in DVC and pursuing the policy of liberlisation are some of the positive steps for the development of this industrial region.
Jute industry is the most important industry of the region. Besides silk & cotton textiles, engineering, electricals, paper, match, chemicals, pharmaceuticals, transport equipment, refining leather, footwear, iron & steel and food processing industry are important industries. Asansol Kulti, Burnapur, Raniganj and Durgapur are important centres of Iran & steel industry.
(2) Mumbai-Pune Industrial Region: Located in Maharashtra from Mumbai to Pune in the south, it is the largest industrial agglomeration in the country. The growth of this region is intimately connected with following factors/events:
- This region also owes its origin to colonial rule since 1774. Britishers took the early initiative and established many industries.
- (The growth and development of Mumbai port as early as 1774 facilitated the import of machinery and other materials and export of finished goods.
- The opening of the first railway track between Mumbai and Thane in 1853, opening of the Bhoghat to Pune and Thalghat to Nasik and opening of the Suez Canal in 1869 led to the development of this region.
- The growth of this industrial region is fully connected with the growth of cotton textile industry in India.
- Availability of cotton due to rich black soil and suitable climate led to the development of cotton textile industry here.
- Being far away from the country’s coal belt it had to develop its hydel power in the Western Ghats (Tata hydro project), atomic power plant at Trambay and some thermal power projects.
- Capital and entrepreneurship was available from Parsi and foreign industrialists.
- The densely populated hinterland (of konkan) provided cheep labour.
- The finding of petroleum in the Bombay High region helped in the development of refining and petrochemical industries.
Besides textiles, electrical goods, leather, engineering, oil-refining, transport equipments, paper, electronics, drugs and food processing are other important industries. Automobile industry has also developed. Besides Mumbai and Pune, other importants centres are Thane, Lalganj, Parel, Kurla, Vile Parle, Andheri, Warli, Nashik, Pipri, Ambernath (arms), Dadar, Trambay, Solapur, Kolhapur, etc. At present, Mumbai region is facing the problem of industrial crowding and congestion.
(3) Ahmedabad-Vadodara Industrial Region: It is the third largest industrial region of the country situated around the gulf of Cambay. It lies in close proximity to the cotton growing tracts of the Gujarat plain. The growth of this industrial region is connected to following factors/events:
- Here industrialisation began with the dispersal of cotton textile industry from Mumbai due to growing congestion in Mumbai and after loss of Chinese market so as to make it closer to the source of raw material and market of Satluj-Ganga plain both.
- Land and the skilled labour available was much cheaper.
- The Kandla port was developed and a good network of rail and road transport was developed to connect the port with the interior.
- The Kandla port provided the export-import facility.
- Completion of Dhuvaran thermal power station, Uttaran gas power station, Ukai hydel project and Kakrapur nuclear power plant provided the much needed power to the industries.
- The discovery and production of petroleum in the Gulf of Combay area the establishment of petro-chemical complex around Ankleshwar and the new port at Kandla had boosting effect on this region.
Today, there are about 9,900 registered factories in this region. Ahmedabad is the largest centre of the region and is the 2nd largest cotton textile industrial centre in the country. Ahmedabad and Vadodara are major centres of chemical and pharmaceutical industry. Oil refineries have been established at Koyali and Jamnagar. Surat is famous for diamond cutting and silk textile. Other important centres are Kalol, Bharauch, Ankleshwar, Anand, Khera, Bhavnagar, Rajkot and Koyali. Other industries include engineering, rayon match, leather, plastic, potteries and glassware.
(4) Madurai-Coimbatore-Bangalore Industrial Region: This region also lies in the cotton growing tract and is dominated by cotton textile industry. It extends from Bangalore in the north to Madurai in the south. Following factors account for its growth:
- This is locoted in such a position that it benefits from the port facilities of both east (Chennai) and west (Mumbai) coast.
- The region is agroclimatically suitable for cotton, silk & sugarcane production.
- The region is rich in minerals (Iron, gold, magnetite, bouxite, etc.).
- The region efficiently harnessed its water power potential by establishing plants like Mettur, Sivasamudram, Papnasam, Pykara and Sharavati projects.
- The transport and communication system are well-developed.
- The hinterland provide a large domestic market.
The region has witnessed industrial diversification housing industries like textiles, sugar, leather goods, chemicals, paper, engineering, machines, electrical equipments, telephone, railway coach, watch making, electronics, etc. Bangalore has important units like HMT watch making, Hindustan Aeronautics, Indian Telephone Industry, Bharat Electronics and Iron & Steel plant (Visvesvaraya). The city has recently emerged as a great centre for electronics and I.T. industry. Coimbatore is known as Manchester of Tamil Nadu. Madurai is known for its cotton textile. Chennai produces cotton textile, vegetable oil and leather goods. Mysore has silk industry. Shivkashi, Tiruchirapalli, Salem, Mandya, Bhadravati and Mettur are other centres.
(5) The Chhotanagpur Plateau Industrial Region: The birth and growth of this region sprawling over Jharkhand and parts of West Bengal, is linked with the discovery of coal in Damodar Valley and Iran are in Jharkhand-Orissa mineral belt.
- Power is available from Damodar Valley corporation’s projects and Thermal Power Plants.
- Surrounding populous states of Bihar, Orissa and West Bengal provide cheep labour.
- The proximity to Kolkata serves two benefits-market & port facility.
- The region is well-connected to Kolkata by rail routes.
In this region, Jharkhand, Durgapur, Aasansol, Bokaro, Kulti, Burnpur and Hirapur are famous for iron & steel industry; Sindri for fertiliser industry, Chittranjan for railway locomotives; Ramgarh & Bhurkunda for glass industry and Khelari for cement industry. Metallurgical and heavy industries account for 47% of the labour force of the region. Ranchi, Dhanbad, Chaibasa. Hazaribagh, Daltanganj and Japla are other important centres. The region is experiencing problems of infrastructural bottlenecks, shortage of power, political instability (law & order) and lack of spread effect. With the creation of new Jharkhand state its importance is bound to grow.
(6) Delhi and Adjoining Industrial Region: This region owes its development to the post independence period. It has the advantage of the proximity to the national capital; availability of cheap raw materials like sugarcane, cotton, sands, wheat bran, etc.; nearness to large consumer market and regular supply of power (from Bhakra-Nangal grid and thermal plants of Faridabad & Harduaganj). This region spreads in two separate belts in north-south direction between Faridabad and Ambala in Haryana and Mathura and Saharanpur in U.P. The capital city has predominance of engineering, electronics, chemical, drugs, textile and consumer industries. Modinagar (textile, engineering), Ghaziabad (synthetic fibre, chemicals, electronics), Shahdara (hosiery), Modipuram (automobile tyre), Faridabad (engineering), Firozabad (glass), Gurgaon (automobiles). Muradnagar (ordinance factory), Meerut (sugar, distillery), and Mathura (oil refinery) are other important centres. The formation of National Capital Region (NCR) has given further boost to the industrial development of the region.
There are numberof minor industrial regions:
- Assam Valley: Tea, food processing , paper, match, silk, oil refining etc.; Guwahati, Digbai, Dibrugarh, Bongaigaon & Tinsukia are important centres.
- Darjeeling Tarai: Tea, Tourism (Darjeeling & Jalpaiguri main centres)
- Bihar-Eastern U.P: Sugar, cement, food processing and engineering; Allahabad, Varanasi (locomotive), Gorakhpur (sugar), Dalmianagar & Patna are centres.
- Indore-Ujjain: Cotton textile, food processing, chemicals, etc.
- Nagpur-Wardha: Cotton textile, engineering, chemical & food processing.
- Dharwad-Belgaun: Engineering, cotton textile, rice milling, spice packing.
- Godavari-Krishna Delta: Rice milling, cotton textile, sugar, fish & chemical industries; Gentur, Vijaywada, Rajahmundary & Vishakhapattanam are main centres.
- Kerala coast: Coconut-oil extraction, rice milling, fish packing, rayon, ship building, refining & Chemical industries. Kochi, Ernakulam, Kollam and Kozhikode are important centres.
Q5. Discuss the growth location and distribution of iron and steel Industry in India. (2000)
Answer :
The process of smelting iron for making iron was know to early settlers, as high grade iron are occurs in many localities. The wrought iron pillar at Delhi is more than 1500 years old. The famous wooly steel produced in India used to be exported to the Middle East during the medieval periods for making Damascus blades.
Growth: An attempt at making iron and steel was begun at Porto Novo In Tamil Nadu in 1830. During the next thirty years similar attempts were made in Utter Pradesh (Kaladhungr). These early attempts were not successful. Pig iron was first successfully produced at Kulti in West Bengal by Bengal Iron Company. In 1900, the production of iron was only 35,000 tonnes. Most of our requirements used to be imported.
The starting of Tata Iron and steel co. in 1907 at Sakchi, (now called Jamshedpur) marked an important stage in iron and steel making in India. This factory first produced pig iron in 1911 and steel in 1913. The first world war gave encouragementfor opening two new units as imports were difficult. The Indian Iron and steel co. was set up at Burnpur in 1919 and Mysore Iron and Steel co. (Now called Visveswaraya Iron and Steel ltd.) was established atBhadrawati in Karnataka in 1923.
Realizing the importance for Iron and steelas a basic raw material the second Five year plan made provisions for starting three large integrated steel plants at Rourkela (Orissa). Bhilai (M.P.) and Durgapur (W.B.) with a capacity of 1.0 Million Tonnes each. Foreign capital and Technology were utilized as in Bhilai (USSR). Durgapur (UK) and Rourkela (Harmony).
During third plan expansion of three private sector companies took place. The process of dispersion continued with new plant at Bokaro, with the help of USSR. During Fourth Plan, three new plants were proposed at Salem (Tamil Nadu), Vijaynagar (Karnataka) and Vishakhapatanam (A.P.). In 1975 steel Authority of India Ltd. (SAIL) was created to manage integrated steel plants of Bhilai, Durgapur, Rourkela, Bokaro, Burnpur and Salem.
The stress on expansion has continued in the subsequent Five Year Plans. Focus is on technology upgradation and establishment of mini steel plants. The ninth plan proposes seventeen new steel plants with combined capacity of eleven million tonnes. The government proposed to increase the production of steel to 60 million tonnes by the end of the plan.
Location and distribution of the industry: The location and distribution pattern of Iron and steel Industry is influenced by the raw materials (Iron ore and Coal), market and sea port facilities. Iron and steel Industry is a weight loosing industry so its localization has been greatly affected by the availability of raw materials. The important raw materials needed in this industry are Iron ore, coke (coal), limestone, mangnese, water and scrap. Iron ore and coal are the bulkiest and required in the largest quantities, so their availability has greatly affected the localization of iron and steel plants.
Most of the raw materials needed for the industry is found in few specific area. In this respect, the mineral rich region of North estern part of the peninsular India covering the states of Jharkhand, Orissa W.B. and adjoining M.P., Chattisgarh has the largest concentration of steel plants. This region is quite rich in Iron ore, Coal and different minerals used in the Industry.
The Iron and steel Industry of India consists of eleven giant integrated plants, 145 mini steel plants and a no. of solling mills and foundries. The major steel plants are discussed below:
- TISCO, Jamshedpur: The Tata Iron and steel Co. Ltd. Is located at Jamshedpur in Singhbhum district of Jharkhand where all the raw material are obtained within 175 km. from the plant site. Iron ores of high grade are obtained from Noamundi in Singhbhum district and Gurumahisari in Mayurbhanj district (Orissa). Cooking coal is obtained from Jharia, manganese from Joda mines in Keonjhar district, limestone and dolomite from Sundargarh district and abundant water supply from Subarnrekha and Khorkai rivers. As the plant is located on thedirect railway line to Kolkata at a distance of 240 km. the finished products, find a ready market and the port facilities for export.
- Burnpur: The plant has three integrated units located near Asansol about 227 km from Kolkata. Located in the coal mining area, the plant gets iron ore from Gua mines and Mangnese from Balaghat in M.P. water and hydro-electricity are obtained from Damodar Valley Corporation.
- Bhadrawati: Located about 17 km. east of Shimoga in north Karnataka, the plant gets iron ore from Bababudan hills. In Chikmangloor district limestone from the nearby and the power from Sharabati power project. The plant has the advantage of nearness to markets in the Southern state of Tamil Nadu, Karala, Karnataka and Andhra Pradesh.
- Rourkela: Located on the Kolkata-Nagpur railway line in the Sundargarh district of Orissa. The plant gets iron ore from the mine located within 80 km. distance and coal is obtained from Jharia and Bokaro. Limestone and Mangnese are locally available and water supply from the tributaries of Brahmani river.
- (5)Bhilai: Located in Durg district of M.P. on the main railway line of Kolkata-Nagpur. The plant gets iron ore from nearby mines and coal from Korba fields, limestone from Nandini area and mangnese from the adjoining districts. Power is available from Korba thermal power station.
- Durgapur: Located in Burdwan district of W.B. about 170 km. from Kolkata, the plant gets iron ore from New Balani mines in Orissa and coal from Jharia field nearby. Water and Power is available from Damodar valley corporation.
- Bokaro: The plant is located near the confluence of Bokaro and Damodar river in Hazaribagh district of Jharkhand, getting coal from Jharia and Raniganj, iron ore from Kiriburu mines of Orissa, limestone from Palamau district, water supply from Subarnrekha river and power from DVC.
- Salem Steel Plant: Located in the Salem in Tamilnadu, the plant gets iron ore, Limestone and cheap power from the adjoining areas.
- Vijaynagar Steel Plant: Located in Hospet region in Bellary district of Kannataka, the plant enjoy the facility of iron ore from the Hospate region, coal from Kanhan valley (Chattisgarh) and Singareni (AP), Limestone and dolomite from a distance of 200 km. and the water supply and cheap hydel power from Tungbhadra project.
- Vishakhapatnam Steel Plant: This is a sea coast based steel plant, well connected with the coal fields of Damodar valley and iron ore deposits of Bailadila in Chattisgarh. The plant is equipped with modern technology of raw material handling and iron ore processing.
- Other important plants include Daitari steel plant near Paradwip in Orissa and New Dolvi steel plant on the west coast in Ratnagiri district of Maharashtra.
- Besides the large integrated plants there are more than 200 mini steel plants with installed capacity of 12 milion tonnes of crude steel per year. Theseplants are widely dispersed to meet the needs of local markets.
Q6. Discuss the factors for the localisation of either the Cement or the Cotton textile industry in India and analyse the pattern of its distribution. (1999)
Answer :
Cement Industry: Cement is an essential item of modern development due to its indispensability for building and construction work. So much so that its production and consumption may be used as an index of country’s progress. This is a basic industry, making an important contribution to the development of other factory based industry, to the construction industry and even to the development of agriculture. Presently cement is one of the most advanced industries in the country.
The chief characteristics of Indian cement industry are:
- Apart from being capital intensive, the industry, of late, has also become ‘technology-intensive’
- Both the ownership and production base in the industry is fragmented.
- India is the fourth largest cement producing country in the world after China, Japan and U.S.A.
- After the complete decontrol of price and distribution on March 1, 1989 and introduction of other policy reforms after 1991, the cement industry has made rapid strides both in capacity generation and in production technology.
- As on April 30, 2002, there were 124 large cement plants with an installed capacity of 137.03 million tonnes per year.
- Besides there are more than 300 mini cement plants with an estimated capacity of 11.10 million tonnes annually.
- The cement production during 2001-02 was 106.9 million tonnes with a growth rate of 9.52%.
- The export of cement was 5.14 million tonnes in 2001-02.
- However, manpower productivity is low in the industry compared to developed countries.
- The location of the industry is decentralised.
Locational Factors: Availability of raw material, bulk transport facility at reasonable cost and market are the three main localisational factors in India. Two facts related to the nature of industry strongly influence the location of industry:
- The marketable finished foods is about 50% of the weight of the raw materials; that is for the manufacture of 100 tannes of cement 160 tonnes of limestone, 38 tonnes of coal and 4 tonnes of gypsum are required.
- The raw material and the finished are both bulky and weight-losing.
Consequently there is a strong tendency for the industry to be located near the source of raw materials, particularly near limestone areas; which is the most important raw material. Other sources of raw material are sludge and slag.
There are three geographical region having huge reserves of limestones:
- Vindhyan system: Good quality limestone occur here, covering the states of Madhya Pradesh, Maharastra, Rajasthan, Gujrat, Jharkhand and U.P.
- Cudappah system – Reserves are found in Andhra Pradesh, Tamil Nadu, Karnataka and Orissa.
- Tertiary limestone- Doon valley of Uttaranchal, Pir Panjal region of J & K, Kumaon region etc.
Good quality of coal is used both as a source of raw material and power. Good quality of coal is found in the Son Valley, Damodar valley and Godavari basin.
Gypsum which is used in small quantity has its source in Bikaner district. Sea shell found on the coast of Gujrat and Tamil Nadu has strongly influenced the location of Dwarka plant. Sludge obtained from fertiliser plant is responsible for location of Sindri Plant while slag (the waste product of Iron & Steel industry) has influenced the location of Chaibasa and Bhadravati plant.
Apart from these raw materials the other factors responsible for its location are availability of power, transport facility and proximity to market.
Locational Trends: It can be observed that there has been locational changes in the cement industry. The industry firstly developed in the central part of the country around the vindhyan system of mountains including Kaimur, Rajmahal running eastwards from Rajasthan up to Jharkand which contains some of the finest limestone deposit and other building materials found in India. Those mountain ranges meet in Jharkhand, the best coalfield of Indian lying in the states of Jharkhand and Bengal. To the north of Vindhyan, gypsum was found in Rajasthan, in Bikaner region. Bordering the Vindhyans the Ganges valley offered excellent potential consumer market for the cement industry.
The industry in Tamil Nadu, Karnataka and Andhra Pradesh were similarly in fluenced by the availability of limestone from Cudappa system.
But the post-independence era was marked by wider dispersal of industries. This dispersal was brought about by:
- The government policy to decentralise the industry.
- Ever increasing demand for cement for construction purposes particularly in housing.
- Change of source of raw materials from conventional to non-conventional one, e.g. near iron and steel industry having slag as raw material.
- Huge demand by metropolitan centres like Mumbai, Kolkata and Chennai.
Thus the industry come to be located in three places:
- Himalayan region where it has proximity to raw material and market.
- Coastal location
- Near the iron and steel centre
Distribution: Although there is hardly any state in the country which is devoid of cement plant but seven states (Madhya Pradesh, Andhra Pradesh, Rajasthan, Gujrat , Karnataka and Bihar) mostly belonging to Vindhyan and Cudappa belt account for about three-fourth of the installed capacity and production of cement in the country. The table given below shows states wise production and number of cement factories:
States | Factories (No.) | Production (1996) in Lakh tonnes | Percent Of All India Production |
Madhya Pradesh-Chhatisgarh | 14 | 156 | 22.5 |
Andhra Pradesh | 18 | 100 | 18.2 |
Andhra Pradesh | 18 | 100 | 18.2 |
Rajasthan | 10 | 78 | 11.4 |
Gujrat | 10 | 56 | 8.75 |
Tamil Nadu | 8 | 58 | 8.77 |
Karnataka | 8 | 56 | 8.5 |
- Madhya Pradesh- Chhatisgarh: Erstwhile Madhya Pradesh is the leading producer of cement on the country contributing 22.5 percent of the total production. Main plants are located at Jamul, Mandhar (in Chhatisgarh), Satan, Katni, Kaymore, Bannmore ( in M.P.) etc. The states have the advantage of raw material and proximity of the big market of the Ganga Plain.
- Andhra Pradesh: Contributing more than 18% of total cement production of the country, the state has major centres at Peddapalli, Panyon, Mancherial, Karimnager, Vijoywada, Krishna, Vishakhapatnam etc. Plants are mostly located in the Telengana belt (raw material) and along the coast.
- Rajasthan: The states is the third largest producer accounting for over 11% of the national output. Plants are mostly located along the foothills of Aravallis where plenty of limestone occurs. Main centres are Sawai Madhopur, Udaipur, Lakheri, Chittaurgarh, Nimbaheda etc.
- Tamil Nadu: Tamil Nadu has some limestone reserves besides the rich deposits from neighboring Andhra Pradesh and Karnataka. Major plants are at Reddipalayam, Thalaiyuthu, Dalmiapuram, Talukapatti etc.
- Gujrat: The state has considerable limestone reserves. Besides sea shells can also be used as raw material. Major plants are located at Sikka, Dwarka, Porbandar, Vadodara etc.
- Karnataka: Contributing over 8% of the total cement production of the country, the state has major plants at Shahabad, Wadi, Kurkunta, etc.
- Maharastra: The state contributes about 8% of the national output with plants located at Chandrapura, Ratnagiri, Sevari, Manikagarh etc.
- Bihar-Jharkhand: The states have advantage of using limestone (locally available), sludge from fertilizer factory (used in Sindri plant) and slag (used in Chaibasa unit). Plants are located at Dalmianagar, Japla, Chaibasa, Sindri, Khelari, Kalyanpur and Banjari,. The overall production has declined much over the years.
The other producers are Uttar Pradesh (Dalla, Churk, Chunar etc.), Orissa (Rajgangpur, Bargarh), Haryana (Charkhi Dadri) Himachal Pradesh (Rajban and Gogal), Jammu and Kashmir (Wuyon, Srinagar), etc. The given figure depicts the major cement producing centres of India.
Cotton Textile Industry: Cotton textile industry is the largest organised and broad based modern industry of India, contributing about 4% of GDP, 20% of manufacturing value added and one-third of total export earnings. About 16% of the industrial capital and over 20 per cent of the industrial labour of the country is engaged in this industry.
It was the cotton textile industry which provided the base around which modern Indian industrialisation was built. It was the first Swadeshi industry as its development was entirely due to indigenous efforts
The origin of cotton textile industry dates back to 1818 when the first cotton textile mill was established at Fort Gloster near Kolkata. The real beginning was made with the setting up of Mumbai spinning and weaving co. ltd. in 1851, the production started in 1854. India’s Cotton Textile Industry holds the third place among the cotton cloth producing countries in the world, next only to USA, and China. The Indian textile industry is complex in its structure with hand woven khadi sector at one end, the sophisticated capital intensive high speed operations on the other. The intermediate segment consists of highly labour intensive handlooms and medium scale operations of powerlooms. There were total of 1768 textile mills in the country in 1998 of which 3/4 were pure spinning mills and 1/4 were composite mills. The contribution of decentralised sector has increased to a great extent, from a mere 19.31 in 1950-51 to 94.18 in 1999-2000. The following table shows the trend in the production of cotton yarn and cloths:
The Cotton Textile Industry employs the largest number of workers, well over 15 million in which the bulk of share is of decentralised sector consisting of handlooms and powerlooms. The industry exports fabrics, yarn and readymade garments which together rank second in exports from the counrty.
Locational Factors: Several Factors like availability of raw cotton, Market, transport etc. play key role in the localisation of this industry. Cotton as a raw material does not lose its weight much in the process of manufacturing. Cotton mill can be set up at any place irrespective of the fact whether it is cotton growing areas or not. So, now transport and market are more determining factors. This is primarily a market oriented industry for which whole India becomes market. Bihar, U.P. Orissa do not grow cotton but big centres are located here. So, initially this industry developed in cotton growing area like Mumbai and Gujrat, it has witnessed great spatial spread.
The earliest mills were located in the cotton growing areas of Maharastra and Gujrat. Other advantage were favourable climate, Mumbai part for import of machinery, banking facilities, availability of power etc.
Distribution And Localisation:
(1) Maharastra: Maharastra produces 46% of mill cloth and 16% yarn. Mumbai is the largest centre, rightly called ‘cottonpolis of India’. Favourable locational factors are humid climate, port facility helping import of machinery and long staple cotton, cheap power, availability of raw material, cheap labour, financial facility, enterprising entrepreneurs, ready market and good transport.
Other centres are Pune, Sholapur, Kolhapur, Satara, Nagpur etc.
(2) Gujarat: Gujarat is the second largest state, contributing 23% of mill cloth and 8% of yarn production. Here, Ahmadabad is the largest centre. In Gujarat favourable locational factors for cotton industry are-
- Near to cotton growing areas
- Enterprising entrepreneurs
- Good transport
- Cheap power
- Cheap labour, cheaper land prices
- Cheaper products having ready market among vast low income masses
Other centres are Vadodara, Surat, Gandhinagar, Rajkot etc.
(3) Tamil Nadu: It is an important cotton producer leading in south. Though only 6% of mill cloth, it produces 1/3 of yarn. Coimbatore, the most important centre is called Manchester of South India. But mills of Tamil Nadu are of smaller size and give less production. Other centres are Chennai, Madurai, Tirunelveli, Tuticorin etc.
(4) Madhya Pradesh: Cotton is locally grown and locally available coal provides energy. Gwalior, Indore, Ujjain, Bhopal etc. are important centres.
(5) Uttar Pradesh: In Western part, Kanpur is largest centre, known as Manchester of U.P. Other centres are Muradabad, Varanasi, Agra, Bareilly, Lucknow, etc. The state enjoys facilities of large home market, cheap and efficient labour and raw material is not very far off.
(6) West Bangal: The state enjoys locational advantages of vast market, cheap coal from Raniganj, port facility of Kolkata, electricity from D.V.C., network of railways and riverways and cheap labour from Bihar-Orissa region. Kolkata is the most important centre followed by Howrah, Sodepur, Murshidabad, etc. The industry has developed despite the disadvantage that it is away from the cotton growing areas.
Other significant producers are Andhra Pradesh (Hyderabad, Guntur etc.), Kerala (Thiruvasantpuram, Kollam), Bihar (Patna, Gaya, Bhagalpur), Rajasthan (Pali, Beawar, Bhilwara etc.), Punjab, (Amritsar, Ludhiana), Karnataka (Bangalore, Belgaum etc.), Following table shows the statewise production of cotton yarn and cloths in 1995-96:
States | Cotton Yarn (in Percent) | Cotton Cloth (in Percent) |
Maharastra | 15.69 | 46.23 |
Gujrat | 7.44 | 21.42 |
Tamil Nadu | 38.10 | 7.04 |
Uttar Pradesh | 5.10 | 1.82 |
West Bengal | 2.34 | 3.17 |
Madhya Pradesh | 3.52 | 3.69 |
Q7. Examine the importance of industrial estates in India. (1998)
Answer :
The industrial estates programme was started in 1955 following the recommendation of the Small-Scale Industries Board with a view to promote industrialization in the backward areas. Twelve estates were sanctioned at that time, ten of which were entrusted to the State Governments while the development of two estates (one in Naini and other at Okhla) was under the National Small Scale Industries Corporation.
The principal objectives of the programme, varying to some degree with time and place, have been.
- to encourage the growth of small scale industries.
- to shift small scale industries from congested areas to estate premises with a view to increasing their productivity.
- to achieve decentralised industrial development in small townsand large villages.
- To encourage the growth of ancilliary industries in the townships surrounding Major Industrial Undertakings.
In these industrial estates the government provides factory accommodations with well established infrastructural facilities. Its importance can be visualized from the principal objectives discussed above. Apart from that:
- An industrial estate brings a number of units together and thereby facilitates the establishment of common service centres.
- It also facilitates the introduction of modern techniques collective purchase of raw materials and sale of finished goods, joint publicity, etc.
- The industrial estates attempt to give the small firms in the estate an opportunity to avail of the numerous external economies.
- The representatives of advisory and information services, research services, financing services are also attracted to the area because of a cluster of industrial firms.
- Another advantage is in the form of inter-trading between the small firms themselves.
- The member enterprises can avail of the goods and services of each other thereby becoming complementary and inter dependent on each other.
- Initially conceived as a measure to promote small-scale industries, the industrial estates were seen as an important means to ensure the industrial spread and development of backward areas.
- During the third plan, the schemes of industrial estates were classified into three categories:
- Urban Estates
- Semi Urban Estates, and
- Rural estates and worksheds
- According to the sixth plan, there were 662 completed industrial estates providing employment to merely 2.2 lakh people.
- Thus the industrial estates have achieved less than what was expected from them mainly because of:
- Wrong location of the estates
- Inadequate techno-economic surveying
- The estates turned out to be highly capital intensive
- Under utilization of installed capacity.
Q8. Bring out the trends in the development of fertilizer industry in India. (1998)
Answer :
In India, fertilizer industry has its own importance. This is the second important industry of the country after the iron and steel in terms of investment and value of manufactured product. India is the third largest producer of nitrogenous fertilizers and seventh largest producer of phosphate fertilizers in the world.
The fertilizer industry of India has following characteristics:
- In India fertilizer industry is basically raw material oriented.
- Though India has increased the fertilizer production during the five year plans but still it is not self sufficient in fertilizer production and technology.
- There are regional imbalance in the fertilizer production.
- The productivity of the fertilizer industry is low.
- The use of fertilizer in India is disproportionate and it varies from region to region.
- The northern zone is the most deficient zone in fertilizer production followed by the western and Eastern Zone.
Developmental Trends: Fertilizer industry is one of the fastest growing basic industry of the country which has taken rapid strides during recent years. The actual growth of the industry has been the outcome of the post independence period. The commissioning of the public sector plant at Sindri by the F.C.I. in 1951 may be termed as the milestone for the industry. Since then the industry has witnessed steady growth. The green Revolution has accelerated the demands for chemical fertilizers.
The production capacity of nitrogenous fertilizers has increased from modest 85 thousand tonnes in 1951-52 to 122.21 lakh tonnes as on 1st April, 2002 and that of phosphatic fertilizers from 63 thousand tonnes to 53.76 lakh tonnes of P2O5 during the same period. Similarly against the nominal production of 16 thousand tonnes of nitrogen and 11 thousand tonnes of P2O5 in 1951-52 the country produced 107.68 lakh tonnes of nitrogen and 38.60 lakh tonnes of P2O5 during 2001-2002. Despite massive increase in the capacity and production of fertilizers over the years, substantial imports are required every year to meet the country’s growing demand. Following table shows the consumption, production and important fertilizer from 1995-1996 to 2001-2002:
At present there are 67 major fertilizer units which includes 39 units producing urea and 9 units producing ammonium sulphate as a by product. Besides there are 80 units producing single superphosphate. Over two thirds of the production capacity lies with the public sector companies. Some important public sector undertakings worthy of mention have been discussed below to highlight trends of development in fertilizer industry.
- The Fertilizer Corporation of India (FCI): Established in 1961 with a view to bring all public units under the management of single undertaking, FCI now has four units at Sindri, Gorakhpur, Talcher and Ramagundam (A.P.), with a total installed capacity of 5.87 lakh tonnes of nitrogen. Only Sindri unit is currently working.
- The National Fertilizer Limited (NFL): Incorporated in 1974, it has six operating units, viz., nitrate plant at Nangal and the urea plants at Nangal, Bhatinda, Panipat, Bijaipur-I and Bijaipur-II extension. The total installed capacity has gone up to 15.66 lakh tonnes of nitrogen, equivalent to 32.31 lakh tonnes of urea and 3.20 lakh tonnes of CAN.
- Later on FCI and NFL were reorganised and four companies on the basis of feedstock and geographical considerations came into existence form April 1978.
- Hindustan Fertilizer Corporation (HFC): Formed in 1978, it has five operating units, three at Namrup in Assam and one each at Durgapur (W.B.) and Barauni, with a total installed capacity of 4.24 lakh tonnes of Nitrogen.
- The Rashtriya Chemical and Fertilizers Limited (RCF): It was also set up in 1978. It is currently operating five fertilizer plants at Trombay set up during the period 1965-82. Prior to 1980 nitrogenous fertilizer plants were based mainly on naptha and fuel oil as feedstock. With free gas being available from offshore Mumbai high, it was decided in 1980 that gas would be preferred feedstock in all future urea plants and for the production of nitrogenous fertilizers. Accordingly a large gas-based fertilizer plant was set up at that under RCF.
- The Fertilizers And Chemicals Travancore Limited (FACT): It has three operating units one at Udyogmandal and two at Kochhi with the commissioning of a caprolactam plant in October 1990, the company has entered the field of petro-chemicals also. FACT engineering and Design Organisation (FADO), another division of the company is engaged in design, engineering, procurement, supervision of construction and commissioning of fertilizers plants.
- Chennai Fertilizers Limited (MFL): Formed in 1966 as a joint venture between Government of India and National Iranian Oil Company, it has annual installed capacity of 3.67 lakh tonnes of nitrogen and 1.43 lakh tonnes of phosphate.
- Pyrites, Phosphates And Chemicals Limited (PPCL): Set up in March 1960, PPCL is presently engaged in the exploration of pyrites deposits as well as production of single-super phosphate at Amjhor in Bihar.
- Paradip Phosphates Limited (PPL): Established in December, 1981 for setting up a phosphatic fertilizer complex at Paradip, Orissa. Its second phase has started commercial production from June, 1992. Recently most of the governments share has been disinvested in February, 2001.
- Projects and Development India Limited (PDIL): It is engaged in design, engineering, procurement and supervision of construction/commissioning of fertilizer and allied chemical plants. The company has played a pioneering role in developing the know-how for the manufacture of catalysts in India.
Cooperative Sector: Indian Farmer’s Fertilizer Cooperative limited (IFFCO) incorporated on 3rd November, 1967 and Krishak Bharati Cooperative Limited (KRIBHCO) is corporated on 17 April, 1980, are multi-state cooperative societies under the administrative control of the Department of Fertilizers. IFFCO has six operating units, one each at kalol and Kandla in Gujarat and Phulpur, Phulpur expansion. Aonla and Aonla expansion in Uttar Pradesh. KRIBHCO has a gas-based urea-Amonia plant at Hazira in Gujarat with a capacity to produce 17.29 lakh tonnes of Urea.
Private Sector: Some of the important private sector fertilizer companies are Chambal Fertilizers and Chemicals, Godepan, Oswal Chemicals and Fertilizers, Paradip, Indian Explosives Limited (IEL), Kanpur, etc.
New Proposals: The Government is considering new proposals valued at Rs. 6973 crores from private sector enterprises and cooperatives. These include National Fertilizers expansion of its Nangal and Panipat plants, KRIBHCO’s expansion of its Hazira plant and a new urea plant at Gorakhpur, IFCO’s grass roots urea plant at Nellore and Kandla expansion project and RCF’s Thai plant expansion. The government is encouraging fertilizer units to enter into joint ventures with buy back arrangements in other countries having rich reserves of natural gas and rock phosphate.
Q9. Growth of agro-based industries in Uttar Pradesh and Bihar. (1998)
Answer :
In the absence of minerals in Uttar Pradesh and Bihar, it is natural that the leading industries should be based on agricultural raw materials. As agricultural crops are almost evenly distributed in this region, industries based on them are generally dispersed, especially sugar, oil mills and rice milling. Cotton and jute textiles, however, tend to cluster in a few towns.
Manufacture of canesugar is the principal industry of Uttar Pradesh and Bihar. The successful attempts of modern sugar industry in India was made in north-eastern Uttar Pradesh and adjoining Bihar. Both states together accounted for rearly half of the total sugar produced in the country in 1969-70. The region benefitted from the local availability of sugarcane. However their share has declined to 28.1% in 2000-01, mainly due to rise of southern states in the sugar production. Still Uttar Pradesh is the second largest producer of sugar. Saharanpur, Meerut, Ghaziabad, Baghpat, Muradabad, Gorakhpur, Deoria, Basti, Gonda etc. in Uttar Pradesh and Saran, Champaran, Muzaffarpur, Siwan etc. in Bihar are important centres of sugar production.
Sugar production is relatively expensive due to low yield of cane/unit area and shorter crushing season. This coupled with obsolete machinery may inhibit the further growth of sugar industry in this region.
Cotton textiles, another agro-based industry, are centred at Kanpur, Patna, Gaya and Bhagalpur. Kanpur, with 14 mills is the largest centre of this region. Cigarettes are manufactured at Monghyr (Bihar). Tanning of leather and manufacture of leather shoes are important industries at Kanpur and Agra. All other agro-based industries are located in the areas which produce the required raw materials. Cotton fabrics, however, fall considerably short of needs and a large quantity of cloth manufactured in western India finds market in this densely populated region.
Jute textiles is another agro-based industry having centres at Samastipur, Katihar and Darbhanga in Bihar and Kanpur and Gorakhpur (Shahjanwan) in Uttar Pradesh. Hand knotted woolen exports of exquisite design are made of Mirzapur district and at Bhadohi in Varanasi district. Bhadohi, Gyanpur and Gopiganj in this area are among the major carpet-making centres of India.
Q10. Critically examine the locational pattern and trend of production of forest-based industries in India. (1997)
Answer :
Forests provide us with different types of materials which are used as raw materials for certain industries. Those industries which use forest products are raw materials are called forest based industries. Paper, match, lac, sports goods, plywood, etc. are such industries.
Paper Industry: Paper, a uniquely useful product, preserves information and propagates thoughts. Although the art of paper making was prevalent as a cottage industry during the Medieval period but the first paper mill on modern lines was set up in 1832 at Serampore (West Bengal).
Locational Pattern: Paper Industry in India is mainly raw material based industry. Paper industry uses cellulosic pulp which is prepared from soft wood, bamboo, grasses, bagasse, rags and waste paper. In India bamboo supplies 70% of the raw material for paper industry and grows well in the tropical areas of north-east India, Orissa, West Bengal, Andhra pradesh, Madhya Pradesh, Maharashtra, Karnataka and Tamil Nadu. Sabai grass, grown in the Tarai region also provides raw material for paper mills.
The states of West Bengal, Andhra Pradesh, Orissa, Maharashtra, Karnataka and Gujarat account for over 70% of the installed capacity and production of paper in the country. Tamil Nadu, Haryana, Uttar Pradesh, Bihar, Kerala and Assam together contribute about 25% of the output of the paper. Since paper and paper board manufacturing uses coarse, cheap and weight losing raw material, there is strong tendency among the paper mills to be located near the forest tract along the Western Ghats, Eastern Ghats, Central India and the Tarai-Bhabar area at the foot hills of the Himalayas. Some of the paper mills are located near the market where cheap labour is also available.
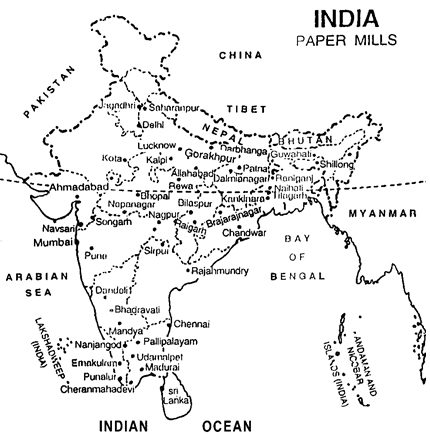
Trend of Production: There is significant improvement in the installed capacity and production of paper and paper baord in the country, exhibiting about 29 and 25 times growth between 1950-51 and 1999-98. The country is almost self-sufficient in respect of common variety of paper and paper board.
Match Industry: Match making can be done in modern factories and at cottage and household industries. In India the first match factory was started at Ahmedabad in 1921. At present the industry involves a productive capital of Rs 6 crore and provides employment to over 3 lakh persons.
The chief raw materials used in this industry are soft timber and paper for making sticks and boxes. Timber is obtained from soft wood trees like dhup, didhu, bakota, semal, salai, poplar etc. which grow in the Andman-Nicobar islands and different parts of peninsular. Majority of the chemicals used in this industry are imported. Match factory requires cheap and skilled labour because one-third of the cost of manufacturing match is on labour.
WIMCO and AMCO are the major companies involved in the match industry. The former was set up in 1923 with five factories located at Ambarnath (Mumbai), Kolkata-Dhubri, Chennai and Bareilly, together contributing about 30% of national output.
Besides, there are over 1000 units in non-mechanised small-scale sector which together contribute 60% of the total production. West Bengal, Tamil Nadu, Maharashtra and Gujarat are main producers.
West Bengal has the highest concentration of match industry. Timber is obtained from Andaman and Nicobar islands as well as from the Sunderbans. The region has the facility of good port of Kolkata for importing chemicals and dense population providing cheap labour.
The cottage sector has more than 6000 units mainly centres in Tamil Nadu are Ramnathpuram, Chinghput, Tiruvelveli and Chennai. The other producers are Maharashtra (Pune, Thane, Mumbai), Gujarat (Ahmedabad, Petlad), Uttar Pradesh (Bareilly, Meerut, Allahabad, Varanasi), Kerala (Thiruvananthpuram) and Assam (Dhubri).
The government is giving incentive to small and cottage industries. Accordingly new units under cottage industrial sector have been set up by the Central Social Welfare Board.
Lac Industry: Lac is a natural resin secreted by insect thriving on the trees of Kusum, Pipal, Babool etc. in areas at an elevation of around 300 metres and having temperature of about 12°C and annual rainfall of about 150cm. About half of country’s production of lac comes from the Chhotanagpur region of Jharkhand. The remaining 50% is produced by adjoining areas in West Bengal (Murshidabad, Malda), Madhya Pradesh-Chhatishgarh (Bilaspur, Raipur, Jabalpur, Shahdol, etc.), Uttar Pradesh (Mirzapur & Sonbhadra), Orissa (Mayurbhanj, Bolangiri, Sambalpur, etc.) Meghalaya (Garo, Khasi and Jayantia hills), Assam, etc.
The average annual production of lac in India is 20-25 thousand tonnes. Earlier India used to produce about 85% of the world’s total but its share has fallen to 50-60% due to increased production in Thailand, Myanmar and Indo-China.
Sports Goods Industry: After partition, newfactories of sports goods were set up at Jalandhar and Meerut. Today there are more than 700 large, medium and small units engaged in the manufacture of sports goods in the country. There together produce sports goods worth of about Rs 50 million and provide employment to about 25,000 persons.
Today, India is in a position to manufacture goods for almost all the sports. The factors contributing to India’s progress are the availability of raw materials and skilled, cheap and abundant labour. Merrut and Jalandhar dominate the production of sports goods. Other important centres are Amritsar and Batala (Pubjab); Moradabad, Modinagar, Lucknow, Allahabad and Bulandshahar (Uttar Pradesh), Katni and Bhopal (Madhya Pradesh); Jammu and Srinagr in J&K; Mumbai and Pune in Maharashtra; Chennai in Tamil Nadu and Kolkata in West Bengal.
Q11. Analyse the factors for the localization of either the cotton textile or the sugar industry in India and note the recent trends in the industry. (1997)
Answer :
Cotton Textile Industry: Cotton textile industry is the largest organised and broad-based modern industry of India, contributing about 4% of GDP, 20% of manufacturing value added and one-third of total export earnings. About 16% of the industrial capital and over 20 per cent of the industrial labour of the country is engaged in this industry.
The origin of cotton textile industry dates back to 1818 when the first cotton textile mill was established at Fort Gloster near Kolkata. The real beginning was made with the setting up of Mumbai Spinning and Weaving Co. Ltd. in 1851, the production started in 1854. India’s Cotton Textile Industry holds the third place among the cotton cloth producing countries in the world, next only to USA, and China. The Indian textile industry is complex in its structure with hand woven khadi sector at one end, the sophisticated capital intensive high speed operations on the other. The intermediate segment consists of highly labour intensive handlooms and medium scale operations of powerlooms. There were total of highly labour intensive handlooms and medium scale operation of powerlooms. There were total of 1968 textile mills in the country in 1998 of which 3/4 were pure spinning mills and 1/4 were composite mills. The contribution of decentralised sector has increasd to a great extent, from a mere 19.31 in 1950-51 to 91.18 in 1999-2000. The following table shows the trend in the production of cotton yarn and clothes:
The cotton textile industry employs the largest number of workers, well over 15 million in which the bulk of share is of decentralised sector consisting of handlooms and powerlooms. The industry exports fabrics, yarn and readymade garments which together rank second in exports from the country.
Locational Factors: Several factors like availability of raw cotton market, transport etc. play key role in the localisation of this industry. Cotton as a raw material does not lose its weight much in the process of manufacturing. Cotton mill can be set up at any place irrespective of the fact whether it is cotton growing areas or not. So, now transport and market are more determining factors. This is primarily a market oriented industry for which whole India becomes market. Bihar, U.P., & Orissa do not grow cotton but big centres are located here. So, initially this industry developed in cotton growing areas like Mumbai and Gujarat, it has witnessed great spatial spread.
The earliest mills were located in the cotton growing areas of Maharashtra and Gujarat. Other advantages were favourable climate, Mumbai port for import of machinery, banking facilities, availability of power etc.
Distribution and Localisation:
Maharashtra: Maharashtra produces 46% of mill cloth and 16% yarn. Mumbai is the largest centre, rightly called ‘cottonpolies of India’. Favourable locational factors are humid climate, port facility helping import of machinery and long staple cotton, cheap power, availability of raw material, cheap labour, financial facility, enterprising entrepreneurs, ready market and good transport. Other centres are Pune, Sholapur, Kolhapur, Satara, Nagpur etc.
Gujarat: Gujarat is the second largest state, contributing 23% of mill cloth and 8% of yarn production. Here Ahmedabad is the largest centre. In Gujarat favourable locational factors for cotton industry are:
- Near to cotton growing areas
- Enterprising entrepreneurs
- Good transport
- Cheap power
- Cheap labour, cheaper land prices
- Cheaper products having ready market among vast low income masses
Other centres are Vadodara, Surat, Gandhinagar, Rajkot etc.
Tamil Nadu: It is an important cotton producer, leading in south. Though only 6% of mill cloth, it produces 1/3 of yarn. Coimbatore, the most important centre is called Manchester of South India. But mills of Tamil Nadu are of smaller size and give less production. Other centres are Chennai, Madurai, Tirunelveli, Tuticorin etc.
Madhya Pradesh: Cotton is locally grown and locally available coal provides energy. Gwalior, Indore, Ujjain, Bhopal etc. are important centres.
Uttar Pradesh: In western part, Kanpur is the largest centre, known as Manchester of UP. Other centres are Muradabad, Varanasi, Agra, Bareilly, Lucknow etc. The state enjoys facilities of large home market, cheap and efficient labour and raw material is not very far off.
West Bengal: The state enjoys locational advantages of vast market, cheap coal from Raniganj, port facility of Kolkata, electricity from D.V.C., network of railways and riverways and cheap labour from Bihar-Orissa region. Kolkata is the most important centre followed by Haara, Sodepur, Murshidabad, etc. The industry has developed despite the disadvantage that it is away from the cotton growing areas.
Other significant producers are Andhra Pradesh (Hyderabad, Guntur etc), Kerala (Thiruvanantpuram, Kollam). Bihar (Patna, Gaya, Bhagalpur), Rajasthan (Pali, Beawar, Bhilwara etc). Punjab (Amritsar, Ludhiana), Karnataka (Bangalore, Belgaum etc).
Sugar Industry: Sugar industry is the second most important agro-based industry in the country. India is largest producer of both sugarcane and canesugar in the world. About 1/4th of world sugarcane and 8% of sugar is produced in the country. Besides, Khandsari and gur are also prepared from sugarcane. This industry provides employment for more than 4 lakh persons directly and a large number of farmers indirectly.
Sugarcane plant is considered to be a genus from India and the art of making gur and khand is prevalent in the country since ancient days. The development of the industry on modern lines dates from 1903 when a sugar mill was started in Bihar. The industry got a boost in 1931 with the imposition of tariff duty on the import of sugar.
Location of the Sugar Industry: Sugarcane is a weight-losing crop, sugar produced from it ranges from 9 to 12 per cent of the weight of the cane. Cane is more difficult to transport than sugar. Further, its sucrose content begins to deteriorate after it has been cut from the field, and better recovery is dependent upon its being crushed within 24 hours of its harvesting. Besides, the price of sugarcane constitutes 52% of the total cost of white sugar. Therefore sugar factories are located within the cane producing regions of the country.
The cane producing belts are the great norhtern plains and Peninsular India. The southern states enjoy more favourable climatic conditions for the cultivation of sugarcane. Maharashtra, Uttar Pradesh, Tamil Nadu, Karnataka, Gujarat and Andhra Pradesh are major sugar producing stats in the country. The first two together produce nearly two-thirds of the total sugar of the country.
Sugar Industry in South-India: Maharshtra has emerged as the leading sugar producer in the country. At the same time, Tamil Nadu, Karnataka and Andhra Pradesh have increased their share. They together produced 59.1% of the total production in 2000-01. It was only 40.5% in 1964-65.
Maharashtra produces more than 1/3rd of the total production of sugar in the country and thus ranks first. There are 119 sugar mills in the state in a narrow belt running from Manmad in the north of Kolhapur in the south. The irrigated black soil tracts of the Godavari, Pravara, Nira and Krishna rivers in the districts of Ahmadnagar, Kolhapur, Pune, Satara, Sangli, Solhapur, Nashik, Aurangabad and Manmad are well-suited to sugarcane cultivation and have the largest concentration of sugar mills. Moreover, due to marine impact the recovery rate of sucrose is higher (11.6%) and the crushing season longer (162 days).
In Tamil Nadu, sugar factories are located in Coimbatore, Vellore, Tiruvanamalai, Villupuram and Tiruchirapalli districts. The state produces 8.3% of total sugar production of the country. Contribution of Karnataka is 8.1%; here sugar factories are located mainly in Belgaum, Bellary, Mandya, Shimoga, Bijapur and Chitradurga districts. Sugar industry in Andhra Pradesh is distributed in the coastal regions, which possesses suitable climatic conditions for sugarcane.
Sugar Industry in North India: Uttar Pradesh is now second in the production of sugar in the country. Its proportion in total production declined from 38.9% in 1964-65 to 26.5% in 2000-01. It has 104 mills mostly concentrated in two belts—The western belt of Ganga-Yamuna Doab and the Eastern belt of Tarai region. Major sugar producing centres in the Ganga-Yamuna Doab are Saharanpur, Muzaffarnagar, Meerut, Ghaziabad, Baghpat, Muradabad and Bulandshahar districts; while Gorakhpur, Deoria, Basti, Gonda, Sitapur, Behraich and Faizabad are important sugar producing districts in the Tarai region.
Sugar factories are located in Bihar, Punjab, Haryana, Madhya Pradesh and Gujarat. Bihar’s contribution has declined from 12% in 1964-65 to mere 1.6% in 2000-01. Saran, Champaran, Muzaffarpur, Siwan, Darbhanga and Gaya districts are important for Sugarcane. Gurdaspur, Jalandhar, Sangarur, Patiala and Amritsar are major producers in Punjab. In Haryana sugar factories are located in Karnal, Ambala, Rohtak, Hissar and Gurgaon districts. Sugar industry is comparatively new in Gujarat. Its share in country’s production increased from only 1.5% in 1964-65 to 5.9% in 2000-01. There are 16 sugar mills located in the cane growing tract of Surat, Junagarh, Rajkot, Amreli, Valsad and Bhavnagar districts.
In recent years, there has been fluctuating trend in the output of sugar and the industry is infested with many problems like non-renumerative price to farmers, sick and uneconomic mills, low yield, shor crushing season, etc.
Q12. Recent changes in India’s basic industrial policy. (1995)
Answer :
A major shift in the industrial policy was made by the Congress (I) Government led by Mr. Narsimha Rao in July 1991. The main aim of this policy was to unshackle the country’s industrial economy from the cobwebs of unnecessary bureaucratic control, introduce liberalisation with a view to integrate the Indian economy with the world economy, to remove restrictions on foreign direct investment and also to free the domestic entrepreneur from the restrictions of MRTP Act. Besides, the policy aims to shed the load of the public enterprises which have shown a very low rate of return or are incurring losses over the years. Following are the important changes effected by this policy:
- Industrial licensing would be encouraged in high priority areas.
- Foreign investment would be encouraged in high priority areas.
- Government would provide automatic approval for technology agreements for technological dynamism.
- Relaxation of MRTP Act which has almost been rendered non-functional.
- Dilution of Foreign Exchange Regulation Act (FERA) making rupee fully convertible on trade account.
- Disinvestment of Public Sector units shares.
- Closing of such public sector units which are incurring heavy losses.
- Abolition of CCI and wealth tax on shares.
- General reduction in customs duties.
- Provide strength to those public sector enterprises which fall in reserved areas of operation or in high priority areas.
- Constitution of special boards to negotiate with foreign firms for large investments in the development of industries and import of technology.
In case you still have your doubts, contact us on 9811333901.
For UPSC Prelims Resources, Click here
For Daily Updates and Study Material:
Join our Telegram Channel – Edukemy for IAS
- 1. Learn through Videos – here
- 2. Be Exam Ready by Practicing Daily MCQs – here
- 3. Daily Newsletter – Get all your Current Affairs Covered – here
- 4. Mains Answer Writing Practice – here